High Pressure Hydraulic Cement Grout Plants
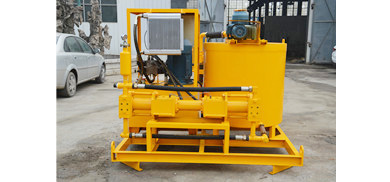
Typically, grout mixers, agitators, pumps, and auxiliary equipment are grouped to create a single large plant or one or more small grout plants. Automated plants,which offer potential advantages in material and labor costs for large projects, are coming increasingly into use. For example, an automated grout plant used during construction of Teton Dam in southeastern Idaho required only one operator for batching neat cement grout; it enabled mixing of a 284-L batch to be accomplished every 45 s and injection of up to 113 m3 of grout in a single shift (Aberle1976). The measurement of batching quantities was accomplished by timing the delivery of each ingredient from the bins to the mixers. The delivery system was arranged so that, by means of a pivoting conveyor belt, three mixers could be used. The quantities of materials fed to each mixer were recorded continuously on a strip tape, using an electronic printer. There are three basic types of grout plant:stationary (or central) plants, modular (or containerized) plants, and "bag" 18 plants.i.e., those in which cement supplied in bags is placed in the mixers manually.Regardless of the type of plant, it is essential that the plant operators be provided with direct radio contact with personnel at the injection and monitoring locations.
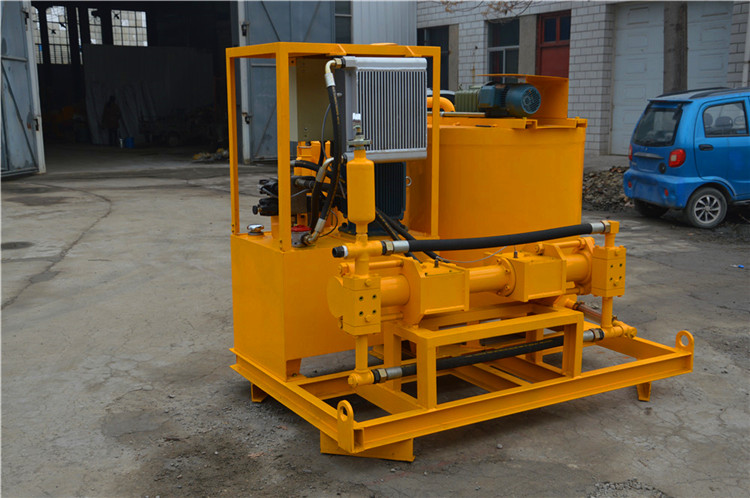
Centrally located stationary grout plants containing several groups of mixers, agitators, pumps, and auxiliary equipment sometimes are set up in enclosed structures at large sites. Grout plants of this type can be especially appropriate for use if large grout takes are expected and if the scope of the work requires that grouting proceed at multiple locations concurrently. in these plants, each equipment group includes automated batching equipment and may include automated recording equipment. Grout produced by centrally located plants may be pumped to distant "satellite" agitators adjacent to the injection locations. Provision may be made for modifying the grout formulation at these satellite locations.
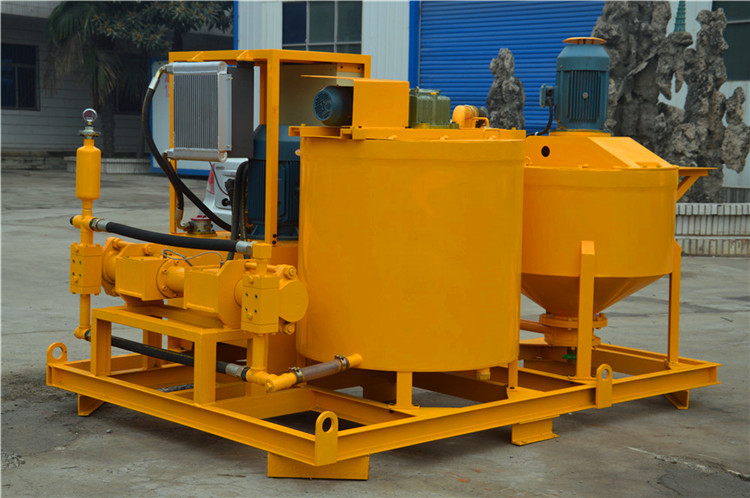
The optimum location for a grout plant for large projects often is at the top of the abutment. This location minimizes delays due to interference with other construction operations and allows delivery of grout from the mixers to portable agitators to take place by gravity. Good road access is essential for delivery of materials, and ample room should be provided for protected storage of those materials. The location should be sufficiently large and flat that a structure can be erected over the equipment to help minimize the extent to which adverse weather will interfere with the operations. Water tanks and storage tanks for hydrated bentonite,preferably each 38 m3 or larger, should be placed adjacent to the building. The hydrated bentonite should be continuously recirculated by a high-capacity pump before use, so that a uniform consistency is maintained.Considerable differences in viscosity will be found between the top and the bot-tom of the tank if small pumps or air-bubbling methods are used for agitation.